How to Replace Transmission Leak Oil Axle Seals Effectively
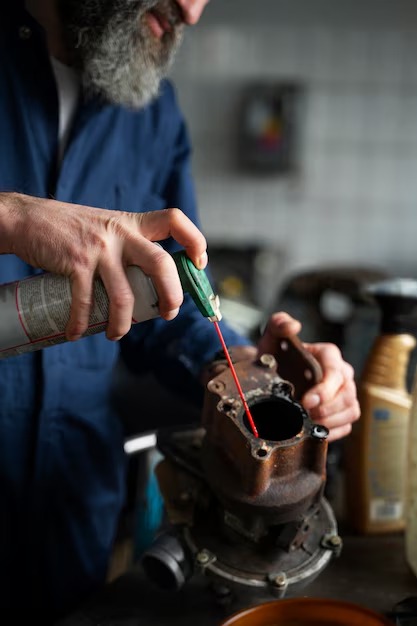
How to Replace Transmission Leak Oil Axle Seals Effectively
The longevity and efficiency of any automobile heavily rely on the proper maintenance of its essential components. Among these elements, certain fixtures play a crucial part in preserving the integrity of the internal mechanisms. Ensuring these crucial parts function optimally is vital in preventing leaks and securing smooth operational performance.
Understanding the process involved in enhancing these fixtures can save time, money, and stress down the line. Adequate preparation, knowledge of required tools, and a systematic approach can lead to a successful overhaul, turning what could be a daunting task into a manageable project. With careful attention to detail, one can ensure that the critical integrity of the vehicle’s functions remains intact.
In this article, we will delve into the essential steps and considerations necessary to conduct this task with the highest degree of accuracy. By following a well-structured guide, individuals can instill confidence in their ability to maintain their automotive machines, ultimately contributing to their performance and durability.
Understanding Transmission Oil Seals Function
In the realm of automotive mechanics, certain components play crucial roles in maintaining performance and longevity. Among these, one must recognize the significance of specific barriers designed to prevent unwanted leakage of vital fluids. Grasping their purpose ensures better management of your vehicle’s overall functionality.
The primary roles attributed to these barriers include:
- Ensuring fluid retention within the system to maintain optimal operation.
- Acting as a safeguard against contamination from external elements.
- Minimizing wear and tear on moving parts, thereby extending service life.
Furthermore, the proper functioning of these components contributes to a quieter and smoother operation, enhancing the overall driving experience. Understanding their role can lead to timely interventions, preventing potential breakdowns and costly repairs.
Key factors influencing the performance of these barriers involve:
- Material quality and resistance to heat and chemicals.
- Proper installation ensuring a perfect fit to avoid gaps.
- Regular maintenance to identify signs of wear, such as cracks or distortion.
Ultimately, recognizing and respecting the function of these essential components aids in sustaining the health of the entire system, allowing your vehicle to perform at its best under various conditions.
Tools Needed for Seal Replacement
Undertaking this type of maintenance task requires a specific set of instruments to ensure a smooth and efficient process. Having the correct gear at your disposal not only simplifies the procedure but also minimizes the risk of errors or damage to components.
Essential tools typically include a wrench set for loosening bolts, screwdrivers for prying or adjusting parts, and pliers for gripping and maneuvering small items. Additionally, a seal puller is crucial for removing old components without causing harm to surrounding areas.
It’s important to have a clean working environment, so a suitable container for catching any residual fluid will also be beneficial. Finally, personal protective equipment such as gloves and safety goggles should be included to ensure safety throughout the task.
Steps for Draining Transmission Fluid
Removing the lubricant from your vehicle’s gearbox is an essential task that ensures the longevity and smooth operation of the system. This procedure involves several key actions that must be performed carefully to prevent any damage and ensure a clean process.
1. Prepare the Workspace: Begin by finding a suitable area to work, preferably on a flat surface. Gather necessary tools such as a wrench, a catch container, and safety gloves to protect yourself during the task.
2. Raise the Vehicle: Use a jack to elevate the car safely, placing jack stands for additional support. This step provides easy access to the undercarriage where the fluid will be drained.
3. Locate the Drain Plug: Identify the specific drain plug on the gearbox. Typically, it’s positioned at the lowest point, allowing the used fluid to flow out efficiently.
4. Remove the Drain Plug: Carefully unscrew the drain plug using the appropriate tool. Be cautious as the fluid may be warm and could spill out rapidly.
5. Allow Complete Drainage: Let the old lubricant fully empty into the receptacle. This process may take a few minutes to ensure all remnants are removed, promoting a cleaner refill later.
6. Clean the Area: After draining, wipe the area around the drain plug to remove any residue. This step helps in preventing contaminants from entering the system when you reassemble.
7. Reattach the Drain Plug: Once drained, securely fasten the drain plug back in place, ensuring it is tight to avoid leaks.
Following these steps ensures a successful removal of the lubricant, paving the way for subsequent maintenance tasks and optimal performance.
Removing Old Seals Safely
Ensuring the careful extraction of worn components is crucial for maintaining the integrity of the entire system. Proper techniques not only prevent damage to surrounding parts but also facilitate a smoother installation of new elements. Following a few important steps can ensure this process is handled with precision.
Preparation and Tools
Before starting, gather essential tools such as a seal puller, scraper, and protective gear. Ensuring that all necessary equipment is at hand will streamline the operation. Additionally, it is paramount to work in a clean, well-lit environment, which minimizes the risk of losing small parts or inadvertently damaging sensitive areas during the removal process.
Safe Extraction Techniques
Begin by assessing the condition of the area surrounding the worn component. Take care not to mar adjacent surfaces, as this can lead to further complications. Utilizing a seal puller allows for controlled extraction, reducing the chance of collateral damage. If necessary, a gentle prying action can assist in loosening stubborn components. Always remain cautious and attentive to avoid accidents during this delicate operation.
Installing New Oil Seals Properly
Ensuring the correct placement of new components is crucial for maintaining the performance of any machinery. This process requires careful attention to detail and adherence to best practices. By following the right steps, one can achieve a long-lasting and efficient function, preventing potential leaks and damage.
Preparation Steps
Before proceeding with the installation, it is essential to gather all necessary tools and materials. Ensure that the working area is clean and free from debris to avoid contamination. Additionally, inspect the housing for any wear or damage that might affect the new component’s function. A thorough cleaning of the surface where the component will be fitted can enhance the seal’s longevity.
Installation Techniques
When placing the new component, align it carefully to avoid misplacement. A gentle tap with a suitable tool may be required to ensure it sits flush with the surrounding surface. It’s advisable to use a lubricant compatible with the materials involved to ease the installation process. After fitting, verify that the component is securely in place and free from any distortions.
Testing for Leaks After Replacement
Ensuring the integrity of the newly installed components is crucial for maintaining optimal performance. It is essential to verify that there are no fluid escapes that could compromise functionality. A systematic approach to inspecting for any signs of leakage can prevent future complications and ensure longevity.
Begin the evaluation by allowing the vehicle to sit idle for a short period. This pause enables necessary components to stabilize and ensures more accurate readings during inspection. Follow this with a thorough check of all areas where the parts have been fitted.
Inspection Method | Description |
---|---|
Visual Inspection | Check around the newly fitted components for any signs of fluid accumulation. |
Pressure Test | Apply pressure where applicable to ensure no fluid escapes under normal operating conditions. |
Dye Test | Introduce a dye into the system and inspect for any discoloration indicating leaks. |
Leak Detector Tools | Utilize specialized equipment to identify even the smallest amounts of escaping fluid. |
After performing these assessments, if any leaks are detected, revisit the installation process to ensure that all components are seated correctly. Timely identification and rectification of leak issues will safeguard overall performance and reliability.
Q&A: Replacing transmission oil seals
What is the purpose of the shaft in an engine?
The shaft in an engine is a critical component that transfers power from the engine to other parts of the vehicle. It helps in converting the rotational energy produced by the engine into usable power for driving the wheels.
How can I fix a damaged shaft in my vehicle?
To fix a damaged shaft, you need to first identify the extent of the damage. If it’s minor, you may be able to repair it by using a specialized shaft repair kit. However, if the damage is severe, replacing the shaft entirely may be necessary for optimal performance.
What are common signs of a failing bearing in an engine?
Common signs of a failing bearing in an engine include unusual noises such as knocking or grinding sounds, decreased engine performance, and metal shavings in the oil. If you notice these symptoms, it’s crucial to address them promptly to prevent further damage.
How do I use a hammer to remove a bearing from a shaft?
To remove a bearing from a shaft using a hammer, you should first ensure that the area is clear and safe. Gently tap around the outer race of the bearing with the hammer to loosen it. Be careful not to damage the shaft during this process; using a bearing puller is often recommended for more stubborn bearings.
What tools do I need to fix a bearing issue in my engine?
To fix a bearing issue in your engine, you will need basic hand tools such as wrenches and sockets, a torque wrench for proper reassembly, and possibly a hammer for removing old bearings. Additionally, having a bearing puller and installation tool can make the job easier.
Can I fix a bent shaft without replacing it?
In some cases, you may be able to fix a bent shaft by carefully straightening it using heat and gentle pressure. However, this method is not always reliable, and if the shaft is significantly bent or weakened, replacement is usually the best option for safety and performance.
What type of bearing is best for high-performance engines?
For high-performance engines, roller bearings are often preferred due to their ability to handle higher loads and reduce friction. They provide better performance under extreme conditions compared to standard ball bearings, making them ideal for racing or heavy-duty applications.
How do I know if my engine’s shaft is misaligned?
You can check for misalignment of your engine’s shaft by inspecting for unusual vibrations during operation, uneven wear on components connected to the shaft, or by using alignment tools specifically designed for this purpose. If misalignment is detected, it should be corrected immediately to avoid further damage.
What happens if I ignore a failing bearing in my engine?
Ignoring a failing bearing in your engine can lead to severe consequences, including complete engine failure. The friction generated by a failing bearing can cause overheating, excessive wear on other components, and ultimately result in costly repairs or even engine replacement.
Is it safe to use a hammer on engine components during repairs?
Using a hammer on engine components should be done with caution. While it can be safe for certain tasks, such as removing bearings or loosening parts, improper use can lead to damage. Always ensure that you are using the right technique and tools to avoid harming sensitive engine components.
How do you fix a transmission pan gasket leak?
To fix a transmission pan gasket leak, you need to drain the transmission fluid, remove the transmission pan using a socket, and replace the old gasket with a new one. Make sure to clean the surfaces thoroughly before reassembly and torque the bolts to the manufacturer’s specifications.
What is the function of the output shaft in a transmission system?
The output shaft is responsible for transferring power from the gearbox to the wheels. It connects the transmission to the drive axles and plays a crucial role in the overall performance of the vehicle’s transmission system.
How can I identify a leaking transmission?
You can identify a leaking transmission by checking for red or brown fluid spots under your vehicle. If you notice that your transmission fluid level is low or if you see fluid leaking from the transmission pan or output shaft seal, it’s time to investigate further.
What steps should I take to replace an output shaft seal?
To replace an output shaft seal, first, drain the transmission fluid and remove the driveshaft. Use a bearing seal remover to extract the old seal, clean the area, and then install a new seal. Reassemble everything and refill the transmission with fluid.
What tools do I need to fix a leaking transmission?
To fix a leaking transmission, you will need basic tools such as a socket set, screwdrivers, and possibly a bearing seal remover. Additionally, having sealant and grease on hand can help ensure proper sealing during reassembly.
How do I know if my gearbox seal needs replacing?
If you notice fluid leaking from the gearbox or if your vehicle is experiencing transmission issues such as slipping or rough shifting, it may be time to replace the gearbox seal. Regularly checking for leaks can help you catch these issues early.
What did Scotty Kilmer say about DIY transmission repairs?
Scotty Kilmer said that DIY transmission repairs can be relatively simple jobs if you take your time and follow proper procedures. Watching videos and researching others’ experiences can provide valuable insights into tackling these repairs effectively.
How do I verify your email address associated with my account?
To verify your email address associated with your account, check your inbox for a verification email. Click on the link provided in that email to confirm your address. If you don’t see it, make sure to check your spam folder.
What is the average cost to replace a seal on a Kooima transmission?
The average cost to replace a seal on a Kooima transmission typically ranges from $10-$15 for the seal itself. However, labor costs may vary depending on whether you choose to do it yourself or hire a professional.
What should I do if my car started leaking transmission fluid after taking a CV joint out?
If your car started leaking transmission fluid after taking a CV joint out, check the output shaft seal for damage. It may have been disturbed during the removal process. If necessary, replace the seal and ensure everything is properly torqued during reassembly.