Guide to Removing and Grinding Valves Seat for Cylinder Head Optimal Engine Performance
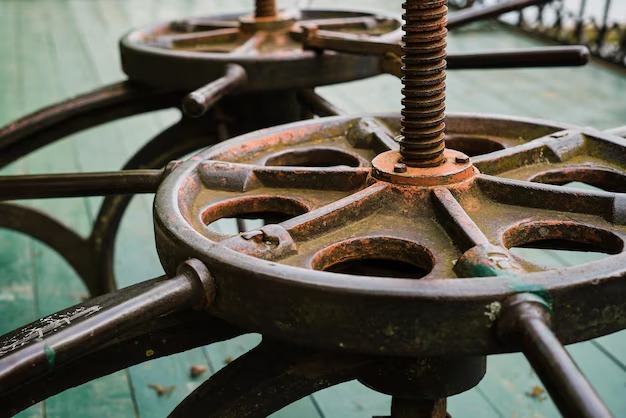
Guide to Removing and Grinding Valves Seat for Cylinder Head Optimal Engine Performance
In the realm of automotive mechanics, the nuances of internal components play a crucial role in the overall function of a vehicles propulsion system. Understanding how to meticulously alter specific elements within this assembly can significantly influence the vigor and efficiency with which an automobile operates. Mastery of these techniques not only contributes to heightened output but also ensures longevity and reliability under various driving conditions.
One of the essential focuses in this pursuit involves refining the interaction between critical parts that facilitate airflow and fuel combustion processes. By implementing advanced methods of adjustment and shaping, technicians can eliminate discrepancies that hinder optimal function. Such corrective measures are vital in achieving a harmonious balance within the mechanical intricacies of a transport unit.
As automotive technology evolves, so too do the strategies employed by professionals. Maintaining an awareness of innovative practices surrounding the fine-tuning of internal components is imperative. This knowledge empowers mechanics to elevate the capabilities of vehicles, resulting in improved responsiveness and an exhilarating driving experience for enthusiasts and everyday users alike.
Understanding Valve Function in Engines
Valves play a crucial role in the operation of combustion units, facilitating the precise management of incoming air and exiting exhaust gases. Their design and functionality directly influence the efficacy of the combustion process and, in turn, the overall capability of the machinery. A thorough comprehension of how these components operate allows for improved optimization and increased efficacy in performance metrics.
Role in Combustion Cycles
Within the cycle of combustion, these components act as gates, opening and closing at specific intervals to allow air-fuel mixtures to enter the cylinder while expelling combustion waste. The timing and synchronization of their operation are paramount, impacting power generation and fuel economy.
Influence on Efficiency
The geometry and finishing of these components can significantly alter airflow characteristics, thereby affecting the energy conversion efficiency. Customization and enhancement of their design can lead to smoother airflow, reduced turbulence, and an overall gain in functional efficacy.
The Importance of Proper Valve Maintenance
Maintaining the components that manage airflow within a combustion unit is essential for ensuring smooth operation and longevity. Regular attention to these critical elements can lead to improved efficiency and reduced risk of costly repairs. Understanding the significance of upkeep in this area is paramount for anyone seeking to enhance their vehicle’s capabilities.
Benefits of Routine Maintenance
- Improved airflow leads to better fuel efficiency.
- Prevention of potential malfunctions or breakdowns.
- Extended lifespan of critical components.
- Enhanced power output and overall responsiveness.
Consequences of Neglect
- Wear and tear can result in decreased performance.
- Accumulation of carbon deposits may lead to efficiency loss.
- Increased emissions and environmental impact.
- Higher costs associated with repairs and replacements.
Prioritizing the upkeep of these essential components not only ensures peak functionality but also contributes to the overall health of the entire machinery. Regular inspections and timely interventions can save time and resources in the long run.
Tools Needed for Valve Removal
In order to effectively engage in the task of extracting critical components from the engine, having the appropriate instruments is essential. Each tool serves a distinct purpose, enabling the mechanism to be accessed with precision and care. Without the right equipment, the process can become challenging, potentially leading to damage or inefficient results.
Essential Instruments
First and foremost, a dependable socket set is required, allowing for various bolt sizes to be addressed comfortably. Ratchets with extensions facilitate accessing hard-to-reach areas. Additionally, a torque wrench ensures that all fasteners are adequately tightened to prevent future issues. A valve spring compressor is crucial for releasing tension safely while handling springs, making it easier to extract parts without causing harm.
Additional Accessories
Included among necessary apparatus are pliers for gripping, a magnet to catch small metallic items, and a cleaning solution to maintain cleanliness throughout the procedure. Utilizing a workbench or a suitable platform enhances stability and organization, providing an efficient workspace. Finally, safety goggles are recommended to protect eyes from debris, ensuring a secure environment while conducting the task.
Step-by-Step Process for Grinding Valves
The procedure of refining components in an internal combustion system is crucial to enhance overall functionality and ensure seamless operation. Proper attention to detail during this task can result in improved efficiency and longevity of the mechanism. Here is a structured methodology to achieve the desired results effectively.
Necessary Tools and Materials
Tool/Material | Purpose |
---|---|
Valving Tool | To hold the part in place |
Cutting Compound | To enhance surface finish |
Measuring Gauge | To check precision and fit |
Cleansing Solvent | To ensure component cleanliness |
Safety Equipment | To protect the operator |
Procedure Overview
Begin by preparing the area and assuring safety measures are in place. Next, position the component securely using the designated tool. Apply the cutting compound evenly and initiate the process carefully, ensuring even distribution of material removal. Regularly check measurements with the gauge to maintain precision. After achieving the desired finish, thoroughly clean the component with a solvent to remove any residual materials. Finally, inspect the piece for quality assurance before reinstallation. This systematic approach will help attain superior results and contribute to a more efficient functioning system.
Signs of Valve Wear and Tear
Understanding the indicators of degradation in critical engine components is essential for maintaining the overall functionality of a vehicle. As these parts age, they exhibit various symptoms that can signal a need for inspection and potential intervention.
- Reduced Power Output: A noticeable decrease in acceleration or overall power can point to underlying issues.
- Unusual Noises: Distinct sounds, such as ticking or knocking, might arise from improper seating or misalignment.
- Increased Fuel Consumption: An unexpected rise in fuel usage may suggest inefficiencies created by compromised components.
- Exhaust Smoke: Excessive smoke from the exhaust can be an indicator of leaks or poor sealing leading to incorrect combustion.
- Engine Misfires: Intermittent engine shuddering or loss of power can be a result of irregular sealing and flow disruptions.
Identifying these signs promptly is crucial, as they can help avert further damage and ensure sustainable operation of the vehicle.
Improving Engine Efficiency through Valve Work
Enhancing the effectiveness of combustion systems relies significantly on the meticulous adjustment of certain critical components. By optimizing these parts, a notable increase in power output and fuel economy can be achieved. Several techniques can be applied to ensure that these components operate at peak efficiency, ultimately leading to a smoother and more responsive driving experience.
Techniques for Enhancing Effectiveness
Various methods can be employed to refine the dynamics of the system. Fine-tuning the shape, size, and seating of internal components allows for improved airflow, reducing restrictions that can hinder performance. Additionally, using superior materials can lead to increased durability and reduced wear over time, thus maintaining efficiency even under extreme conditions.
Benefits of Optimization
The advantages of diligent component adjustment extend beyond just immediate performance boosts. Improved combustion efficiency translates into lower emissions, contributing to a cleaner environment. Furthermore, enhanced throttle response and better torque characteristics can significantly alter the overall driving pleasure, making the vehicle more enjoyable to operate.
Q&A: Removing and grinding valves
What is valve grinding and why is it important in engine maintenance?
Valve grinding is the process of smoothing and finishing the valve face of an engine’s valves to ensure a proper seal when the valve is closed. This process is crucial for maintaining engine performance, as it prevents leaks and ensures efficient combustion.
How does the condition of the valve face affect engine performance?
The condition of the valve face directly impacts engine performance. A worn or damaged valve face can lead to poor sealing, resulting in loss of compression, increased emissions, and reduced power output. Regular valve grinding helps maintain optimal contact between the valve and the seat.
What tools are commonly used in the valve grinding process?
Common tools used in the valve grinding process include grinding machines, lapping tools, and specialized grinding compounds. The grinding machine is used to achieve a precise finish on the valve face, while lapping tools help to ensure an even surface.
Can you explain the lap process in valve grinding?
The lap process in valve grinding involves using a soft material, known as a lap, to polish the valve face against its seat. This method enhances the surface finish and improves the sealing capability of the valve, leading to better engine efficiency.
What types of machines are typically used for valve grinding?
Machines typically used for valve grinding include dedicated valve grinding machines and portable valve grinders. These machines are designed to accurately grind the valve face at specific angles and ensure a smooth finish for optimal sealing.
How often should valve grinding be performed on an engine?
Valve grinding should be performed during regular engine maintenance intervals, especially when rebuilding or overhauling an engine. It’s recommended to check the condition of the valve face and perform grinding as needed to maintain optimal engine performance.
What are the signs that indicate a valve face may need grinding?
Signs that a valve face may need grinding include decreased engine performance, increased oil consumption, unusual engine noises, and a rough idle. If these symptoms occur, inspecting the valve face for wear or damage is essential.
Is it possible to perform valve grinding without a machine?
While it is possible to perform manual valve grinding using hand tools, using a machine is highly recommended for achieving precise results. Machines provide better control over the grinding process, ensuring a uniform finish on the valve face.
What safety precautions should be taken during valve grinding?
Safety precautions during valve grinding include wearing protective eyewear, gloves, and a dust mask to prevent inhalation of fine particles. Additionally, ensuring proper ventilation in the workspace is important to minimize exposure to harmful dust and fumes.
How does improper valve grinding affect the longevity of an engine?
Improper valve grinding can lead to uneven surfaces on the valve face, resulting in poor sealing and increased wear on the engine components. This can ultimately shorten the lifespan of the engine due to overheating, loss of compression, and increased risk of failure.
What is a valve grinding machine and how does it function in engine repair?
A valve grinding machine is a specialized tool used to grind the valves and valve seats of an engine. It functions by using a grinding wheel to create a perfectly flat surface on the valve face, ensuring that the valve seal is optimal when closed.
How do you grind the valves using a valve grinding machine?
To grind the valves using a valve grinding machine, the valve must be mounted securely, and the grinding wheel is adjusted to the required angle. The machine then removes material from around the valve, creating a smooth surface that enhances contact area with the valve seat.
What is the significance of valve lapping in conjunction with valve grinding?
Valve lapping is significant because it involves applying a fine abrasive paste to further smooth the surface of the valve and ensure that the valves and valve seats have optimal seat contact. This process complements valve grinding by enhancing the overall sealing capability.
What are individually driven grinding heads, and how do they improve the grinding process?
Individually driven grinding heads are components of advanced valve grinding machines that allow each valve to be ground independently. This design improves the grinding process by providing better control and consistency, ensuring that all valves are accurately centered and properly shaped.
How does the condition of the valve stem affect the need for a valve job?
The condition of the valve stem can determine whether a valve job is necessary. If the valve stem shows signs of wear or damage, it may need to be replaced to maintain proper alignment and function during engine maintenance.
What role does the exhaust valve play in engine performance?
The exhaust valve plays a crucial role in engine performance by allowing exhaust gases to exit the combustion chamber. Proper sealing and functioning of the exhaust valve are essential for maintaining compression and preventing back pressure that can hinder engine efficiency.
Why is it important to remove the valve during engine maintenance?
Removing the valve during engine maintenance allows for thorough inspection and repair. It enables technicians to assess the condition of the valve guide and ensure that the contact area between the valve and seat is free from wear or damage.
How does lapping compound differ from grinding compound in valve repair?
Lapping compound is typically finer than grinding compound and is used after grinding to polish the surfaces of the valves and seats. While grinding compound removes material, lapping involves applying a fine abrasive paste to achieve a smoother finish and enhance seat contact.
What safety risks should be considered when using a valve grinding machine?
When using a valve grinding machine, safety risks include exposure to fine dust from grinding, which can be harmful if inhaled. Proper ventilation, protective eyewear, and masks should be used to mitigate these risks during the grinding process.
How can a professional machine shop assist with valve seat grinding?
A professional machine shop can assist with valve seat grinding by providing specialized equipment and expertise. They can accurately determine the appropriate angle for grinding and ensure that all valves and valve seats are ground to achieve a perfectly flat surface for optimal sealing.