Guide to Checking and Adjusting Valves Clearance for Optimal Engine Performance
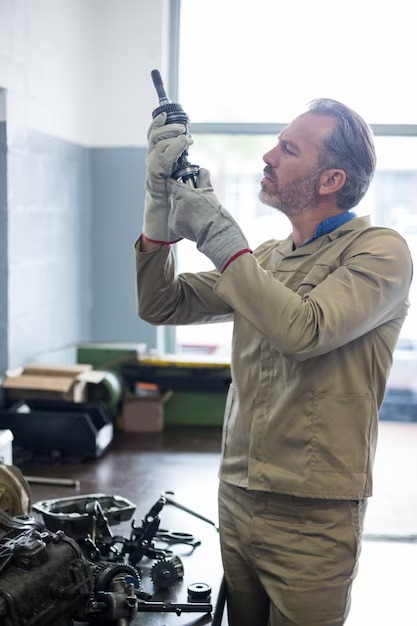
Guide to Checking and Adjusting Valves Clearance for Optimal Engine Performance
Maintaining the superb functionality of an engine requires attention to various components. Among them, certain elements play a crucial role in achieving smooth operations, enhancing fuel efficiency, and prolonging the lifespan of the vehicle. Understanding the significance of regular maintenance can lead to improvements that are not only noticeable but also essential for the longevity of automotive machinery.
Proper maintenance
Engaging in routine evaluations provides an opportunity to gain insights into the engine’s condition. Armed with knowledge about fundamental adjustments, individuals can take proactive measures to rectify any issues. Emphasizing this routine not only enhances the driving experience but also bolsters reliability on the road, making every journey smoother and more enjoyable.
Importance of Valve Adjustment in Engines
The precision of engine operation hinges significantly on the proper alignment and calibration of its internal components. Ensuring these elements function harmoniously can lead to enhanced efficiency, increased longevity, and smoother overall mechanics. Neglecting this aspect may result in a range of issues that affect not just power output, but also fuel consumption and emissions levels.
Optimal synchronization among engine components plays a pivotal role in achieving the desired outcomes. When settings are out of sync, performance drops, leading to greater wear, potential overheating, and inefficient combustion. In turn, this may necessitate costly repairs or even premature replacement of parts.
Regular attention to this crucial aspect safeguards against these adverse effects, promoting a healthier engine environment. By attending to these specifics, one can ensure that the vehicle operates closer to its intended characteristics, thereby enhancing driving experience and operational reliability.
Tools Required for Valve Inspection
Proper maintenance practices necessitate specific instruments to ensure reliable evaluation of mechanical components. Utilizing the correct tools enhances accuracy and aids in diagnosing potential issues efficiently. A well-equipped workspace facilitates a smoother inspection process and guarantees thoroughness.
Essential Instruments
A variety of devices is crucial for effective assessments. Commonly used tools include torque wrenches, feeler gauges, and micrometers. Each of these instruments plays a vital role in determining the condition and alignment of the components being scrutinized. Ensuring precision is key to achieving the desired results.
Safety Equipment
In addition to measurement instruments, it is important to have safety gear on hand. Gloves, goggles, and ear protection help safeguard users during the evaluation process. Prioritizing safety while handling mechanical parts not only protects individuals but also supports a more efficient workflow.
Steps to Check Valve Clearance
Maintaining precise engine function requires meticulous evaluations of gaps in mechanical components. This process ensures that elements operate within designated parameters, enhancing overall efficiency and longevity. Careful examination of these spaces promotes seamless operation and prevents potential issues.
Begin by preparing the workspace and necessary tools. Ensure the engine is cool, and gather a feeler gauge, wrenches, and screwdrivers. Having a manual specific to the engine model can provide crucial insights into correct specifications.
Next, locate the access points to the components needing inspection. Remove any covers or components obstructing visibility, ensuring clarity for the task ahead. Documenting the sequence of disassembly can aid in reassembly.
With access secured, position the engine at the appropriate timing mark to align the components correctly. This step is vital as it ensures that measurements taken indicate true clearances relevant to the engine’s cycle.
Using the feeler gauge, insert it into the spaces between the components. Note the readings carefully, as they must correspond with manufacturer specifications. If gaps diverge from accepted ranges, corrective measures must be considered.
After gathering all necessary measurements, reassemble any removed parts following the documented sequence. Ensure everything is secured tightly, as improper assembly may lead to further issues.
Finally, conduct a brief inspection after reassembly to confirm that all components are in place and functioning as intended. Regular maintenance of these elements fosters better efficiency and can significantly impact the engine’s lifespan.
Common Signs of Valve Misalignment
Recognizing the indicators of misalignment is essential, as early detection can prevent more severe issues down the line. Various symptoms arise when components are not functioning harmoniously, impacting overall efficiency and potentially leading to extensive damage.
Unusual Noises
Audible irregularities during operation are a primary sign that something might be off. Grinding, clattering, or excessive vibrations often signal that components are not properly aligned, requiring immediate attention to avoid catastrophic failure.
Performance Drops
Experiencing a noticeable reduction in efficiency can also point towards alignment issues. Decreased power output or fluctuations in speed may indicate that the components are struggling to work together, leading to suboptimal functioning.
How Temperature Affects Valve Performance
Temperature plays a crucial role in the functionality of mechanical components, influencing their efficiency and reliability. Variations in heat levels can lead to changes in material properties, fluid viscosity, and overall operability, thereby impacting the way these components work in various applications.
As temperatures increase, materials may expand, potentially altering the seating and sealing mechanisms of the devices. This thermal expansion can create gaps or misalignments that compromise efficiency and effectiveness. On the other hand, low temperatures can lead to contraction, which might cause binding or stiction in the moving parts, leading to sluggish operation.
Furthermore, heat can affect the viscosity of fluids moving through these components. For liquids, higher temperatures typically decrease viscosity, allowing for smoother flow. Conversely, cooler temperatures raise viscosity, resulting in sluggish movement and decreased responsiveness. These changes can have significant implications for system performance and system response times.
In addition, the type of material used significantly impacts the performance under temperature fluctuations, as each substance reacts differently to thermal stresses. Selecting appropriate materials that maintain integrity across a range of operating temperatures enhances durability and consistency, ensuring reliable operation in diverse environments.
Finally, temperature influences the longevity and maintenance needs of these devices. Continuous exposure to extreme temperatures may accelerate wear, leading to increased frequency in maintenance tasks or replacements. Understanding these thermal impacts is key to achieving lasting functionality and efficiency in any system.
Regular Maintenance for Valve Longevity
Consistent care is essential for ensuring the durability and efficiency of vital components within various systems. Routine upkeep not only extends the lifespan of these elements but also enhances their overall reliability and functionality. This section highlights key practices that contribute to sustainable operation.
Key Practices for Sustaining Functionality
- Establish a regular inspection schedule to identify potential wear and tear.
- Utilize appropriate lubricants to minimize friction and prevent corrosion.
- Monitor operating conditions to detect any abnormalities in performance.
- Clean all surfaces routinely to eliminate contaminants that may impede function.
Documentation and Record Keeping
- Maintain detailed logs of maintenance activities and any issues encountered.
- Track performance metrics to recognize patterns that may indicate future concerns.
- Review historical data to inform necessary upgrades or modifications.
Implementing these strategies can significantly increase the lifespan and reliability of critical components, ensuring that systems operate smoothly over time.
Q&A: Checking and adjusting valves
What is the function of the exhaust valve in an engine?
The exhaust valve allows exhaust gases to exit the cylinder after combustion, helping to maintain proper engine performance and efficiency.
How does the valve stem contribute to the operation of the exhaust valve?
The valve stem is the part of the valve that extends into the cylinder head, allowing the valve to open and close as the camshaft rotates, controlling the flow of gases in and out of the cylinder.
What role does the cylinder play in an internal combustion engine?
The cylinder houses the piston and is where the combustion process occurs, creating the power needed to drive the vehicle.
How does the camshaft affect the timing of the intake and exhaust valves?
The camshaft controls the opening and closing of both the intake and exhaust valves by rotating and pushing against the rocker arms, ensuring that they operate at the correct intervals during the engine cycle.
What should you do to check the valve clearance in your engine?
To check the valve clearance, you need to remove the valve cover, rotate the engine to TDC (top dead center) on the compression stroke, and measure the gap between the rocker arm and the valve stem using a feeler gauge.
How can you identify issues with the cylinder head?
You can identify issues with the cylinder head by checking for leaks, cracks, or warping. A compression test can also help determine if there are problems affecting cylinder pressure.
What is the purpose of a rocker arm in an engine’s valvetrain?
The rocker arm transfers motion from the camshaft to the valve stem, allowing for precise opening and closing of both intake and exhaust valves during engine operation.
How do you adjust the valve clearance in an engine?
To adjust the valve clearance, you need to loosen the lock nut on the rocker arm, turn the adjusting screw to achieve the desired clearance, and then tighten the lock nut while ensuring that the adjustment remains intact.
What is the difference between an intake valve and an exhaust valve?
The intake valve allows air and fuel mixture to enter the cylinder for combustion, while the exhaust valve allows exhaust gases to exit after combustion has occurred.
How does compression affect engine performance at TDC?
Compression at TDC is crucial for efficient combustion; higher compression ratios can lead to more power and better fuel efficiency, while low compression can result in poor engine performance and difficulty starting.
What is valve lash and why is it important for an engine?
Valve lash refers to the clearance between the rocker arm and the top of the valve stem. It is important because it ensures that the engine valves open and close properly, allowing for optimal engine performance.
How do you check the clearance for valve lash?
To check the clearance for valve lash, you need to remove the cylinder head cover and use a feeler gauge between the rocker arm and the top of the valve stem. This will help you measure the gap between the rocker arm and the valve.
What steps are involved in adjusting the valve clearance?
To adjust the valve clearance, you need to turn the engine to top dead center on the compression stroke, check the clearance measurement, and if necessary, remove the valve buckets to replace or shim them to achieve the correct valve lash.
What tools do you need for a valve clearance adjustment?
For a valve clearance adjustment, you typically need a feeler gauge, a shim kit, a wrench for the adjuster, and engine oil to lubricate moving parts during the process.
What should you do if you find incorrect clearances during your inspection?
If you find incorrect clearances during your inspection, you will likely need to adjust the valve clearance by removing the valve buckets and shimming them to ensure that the tappet clearance is within the recommended specifications.
How do you measure the thickness of shims needed for valve adjustment?
To measure the thickness of shims needed for valve adjustment, you must check the clearance measurement with a feeler gauge and then measure how much thinner or thicker the shim you need to achieve the proper valve lash.
Why is it necessary to rotate the engine during this process?
It is necessary to rotate the engine to ensure that all valves are closed and that you can accurately check and adjust each valve’s clearance without interference from other moving parts inside the engine.
What role do valve springs play in maintaining proper valve function?
Valve springs maintain tension on the valves, ensuring they return to their closed position after being opened. This is crucial for proper operation and helps prevent issues such as incorrect valve lash or misfiring.
How can engine heating affect valve clearance?
As the engine heats up, components expand, which can change the clearance measurement. Therefore, it’s essential to perform a valve clearance adjustment when the engine is at operating temperature to ensure accurate results.
What should you apply to the adjuster during a valve clearance adjustment?
During a valve clearance adjustment, it’s important to apply a small amount of engine oil to the adjuster and other moving parts to prevent wear and ensure smooth operation of the valve train components.