Essential Guide to Servicing a Every Diesel Engine Maintenance Checklist
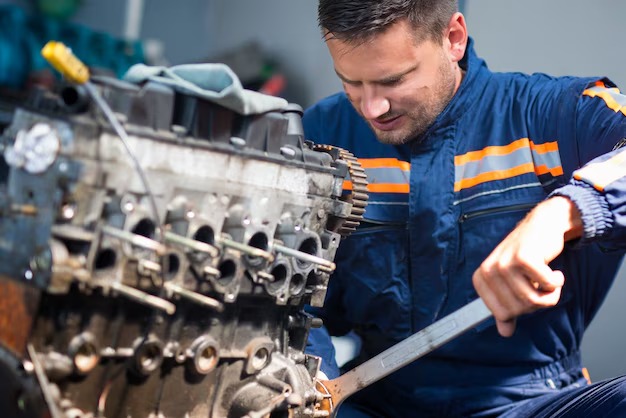
Essential Guide to Servicing a Every Diesel Engine Maintenance Checklist
A well-maintained piece of heavy machinery is vital for optimal performance and durability. Understanding the intricate requirements of these powerful machines can significantly enhance their lifespan and efficiency. This section delves into practical strategies aimed at preserving the functionality of robust machinery utilized in various industries.
Regular inspections and appropriate interventions can prevent minor issues from escalating into costly repairs. Knowledge of the specific requirements of your machinery, including routine checks and changes, is crucial for ensuring seamless operation. This guide provides an overview of pivotal considerations that every operator should keep in mind.
The expertise in handling maintenance tasks can empower operators to make informed decisions, preventing downtime and ensuring peak performance. By adhering to proven strategies, one can cultivate a deeper understanding of their machinery’s needs, ultimately contributing to a more productive work environment.
Understanding Diesel Engine Components
Grasping the fundamental parts of a combustion mechanism is vital for maintaining its efficiency and longevity. Familiarizing yourself with each element’s role and function will enhance your knowledge and allow you to recognize potential issues early on.
Main Parts Overview
Each segment of the system plays a unique function, contributing to its overall performance. Below are the primary components to focus on:
- Fuel System
- Air Intake System
- Cylinders
- Crankshaft
- Exhaust System
- Cooling System
Fuel System Insights
The fuel system is critical for delivering the necessary fuel to the combustion chamber. It includes various parts such as:
- Fuel Tank
- Fuel Pump
- Fuel Injectors
Each part must operate flawlessly to ensure optimal performance and efficiency. Regular checks and maintenance are necessary for these components to function effectively.
Common Maintenance Tasks for Diesel Engines
Regular upkeep is vital for the longevity and efficiency of heavy machinery. Implementing straightforward procedures helps to ensure optimal performance and prevents unnecessary breakdowns. Understanding the key actions involved in maintaining your vehicle can contribute significantly to its reliability and lifespan.
Fluid Checks: Monitoring levels of oil, coolant, and fuel is crucial. Regular inspections can help detect leaks and assure that all fluids are at the proper levels to maintain optimal functioning.
Filter Replacements: Changing air and fuel filters at recommended intervals is essential for blocking contaminants. This not only enhances performance but also prolongs the life of the machinery.
Belt and Hose Inspection: Components such as belts and hoses should be examined regularly for signs of wear, cracks, or fraying. Timely replacement is necessary to avoid sudden failures that could lead to extensive damage.
Battery Maintenance: Keeping the battery terminals clean and performing regular charge checks can prevent startup issues. A well-maintained battery ensures reliable power delivery when needed.
Exhaust System Review: Inspecting the exhaust for any leaks or blockages is important. A clear exhaust system contributes to efficient operation and compliance with emission standards.
Tire Care: Regularly checking tire pressure and tread conditions is part of ensuring safety and performance. Properly inflated tires enhance traction and fuel efficiency.
By adhering to these fundamental tasks, operators can effectively minimize downtime and ensure their machinery operates smoothly and efficiently for years to come.
Signs Your Diesel Engine Needs Attention
Awareness of potential issues in machinery is crucial for maintaining optimal performance. Recognizing early indicators can help prevent more severe complications and ensure that your vehicle operates smoothly. Below are some common signs that your power unit may require further inspection or intervention.
Unusual Noises
Pay attention to any strange sounds coming from the vehicle. These can consist of:
- Knocking or rattling noises
- Hissing or whistling sounds
- Excessive clicking
Such noises often indicate possible mechanical failures or component wear, necessitating a thorough examination.
Visible Smoke
Smoke emissions can provide significant clues regarding the condition of your power device. Monitor the following:
- Black smoke: often signifies poor fuel combustion, possibly due to a clogged air filter or faulty injectors.
- Blue smoke: usually indicates oil consumption, implying wear on piston rings or valve seals.
- White smoke: may mean coolants are leaking into the combustion chamber, suggesting a head gasket issue.
Addressing smoke-related problems immediately can help to avoid further damage.
Fluid Leaks
Keep an eye out for any fluids pooling under the vehicle. Common leaks can be:
- Oil leaks, indicating seal or gasket issues
- Coolant leaks, which may result from damaged hoses or fittings
- Fuel leaks, pointing to fuel line deterioration
Any unexpected liquid beneath the vehicle warrants immediate investigation.
Oil Change Intervals and Importance
The frequency of oil replacement is crucial for maintaining optimal performance and longevity of machinery. Regularly scheduled changes help prevent issues related to lubricant degradation and contamination, ultimately preserving the overall functionality.
Understanding the recommended intervals for oil replacement is essential for ensuring that the lubricant remains effective. Factors such as operational environment, usage patterns, and manufacturer guidelines play a significant role in determining when a change is necessary.
Factor | Recommended Interval |
---|---|
General operation | Every 5,000 – 7,500 miles or 6 months |
Heavy-duty usage | Every 3,000 – 5,000 miles or 3 months |
Extreme conditions | Every 2,000 – 3,000 miles or monthly |
Manufacturer recommendations | As specified in the owner’s manual |
Adhering to these intervals not only enhances performance but also minimizes the risk of component damage. Ignoring oil replacement can lead to increased wear, overheating, and eventual mechanical failure, resulting in costly repairs and downtime.
Establishing a consistent schedule for oil changes, based on usage and environmental conditions, ensures that machinery operates smoothly and efficiently over its lifespan. Therefore, proper maintenance is not just beneficial but essential for reliable operation.
Choosing the Right Fuel for Performance
Selecting the appropriate type of fuel is crucial for maximizing the effectiveness and longevity of your machinery. The right choice not only influences operational efficiency but also impacts overall performance and emissions. Understanding various fuel options available in the market can help ensure that your machinery runs at its peak capability.
Different formulations offer unique advantages, including improved combustion characteristics and reduced particulate matter. It’s vital to familiarize yourself with the specifications that best align with your specific requirements. Some fuels provide enhanced lubricity, while others may include additives designed to boost performance under various conditions.
Additionally, regional factors, such as climate and altitude, can affect fuel choice. Assessing your operational environment can guide you in making an informed decision that complements the working conditions. Regularly reviewing fuel quality and sourcing from reputable suppliers also contributes to maintaining optimal function.
Ultimately, investing time in understanding fuel characteristics tailored to your machinery will yield better performance, reduced maintenance costs, and lower emissions, benefitting both the equipment and the environment.
Tools and Equipment for Diesel Care
Maintaining the performance of a robust power unit requires a set of specialized implements and devices. Proper tools are indispensable for ensuring longevity, efficiency, and reliability. Whether you are a seasoned mechanic or a dedicated hobbyist, understanding the fundamental apparatuses will facilitate effective upkeep of these mechanical systems.
Hand Tools: Basic hand tools such as wrenches, sockets, and screwdrivers are vital for general tasks. These items allow for tight fittings and adjustments, ensuring component integrity. A torque wrench is particularly crucial for applying precise force when securing bolts and screws.
Diagnostic Equipment: Advanced technology, such as diagnostic scanners, can provide invaluable insights into the performance and functionality of the machinery. These devices read error codes and monitor systems, identifying potential issues before they escalate into major problems.
Fluid Management: Proper management of fluids is crucial for operational efficiency. Utilizing oil change pumps and coolant testers helps maintain optimal fluid levels and conditions. Moreover, having storage containers for waste fluids ensures safe disposal and environmental protection.
Safety Gear: Always prioritize safety when working with heavy machinery. Personal protective equipment (PPE) such as gloves, goggles, and ear protection are essential to prevent injuries and ensure a safe working environment.
Cleaning Implements: Regular cleaning of components prevents the buildup of debris and improves overall performance. Equip yourself with brushes, vacuums, and pressure washers designed for tough grime removal.
In conclusion, investing in the right tools and equipment plays a significant role in the upkeep of mechanical systems. Understanding the various implements available enhances your ability to maintain, diagnose, and optimize functionality effectively.
Q&A: Servicing a diesel engine
What type of fuel is primarily used in a diesel vehicle?
Diesel fuel is primarily used in diesel vehicles, which includes trucks and diesel cars. This type of fuel is specifically designed for the combustion process in diesel engines.
How often should I change the oil in my diesel vehicle?
It’s essential to change the oil in your diesel vehicle regularly, typically every 5,000 to 7,500 miles, depending on the manufacturer’s recommendations and your maintenance schedule.
What is the importance of using the right engine oil in a diesel engine?
Using the correct engine oil in a diesel engine is crucial for optimal engine performance. Diesel engine oil contains additives that help reduce wear, prevent corrosion, and maintain proper lubrication under high-stress conditions.
How does a water separator function in a diesel vehicle?
A water separator in a diesel vehicle removes water from the diesel fuel before it reaches the engine. This is important because water can cause corrosion and affect engine performance, potentially leading to severe damage.
What are some maintenance tips for keeping a diesel truck running smoothly?
Regular maintenance tips for a diesel truck include changing the oil and oil filter regularly, checking the water separator, monitoring fuel quality, and ensuring that all filters are clean and free from debris.
How does the maintenance of a gasoline engine differ from that of a diesel engine?
The maintenance of a gasoline engine differs from that of a diesel engine mainly due to the presence of spark plugs in gasoline engines. Diesel engines do not use spark plugs; instead, they rely on compression for ignition, which affects their maintenance requirements.
What should I do if my diesel car experiences a drop in engine performance?
If your diesel car experiences a drop in engine performance, check for clogged filters, ensure that the fuel system is clean, and inspect the water separator for any issues. Regular maintenance can prevent these problems from escalating.
Why is it important to regularly check and replace the oil filter in a diesel vehicle?
Regularly checking and replacing the oil filter in a diesel vehicle is important because a clogged filter can restrict oil flow, leading to increased wear and potential engine damage. This is vital for maintaining engine performance.
What role does corrosion play in the maintenance of a diesel engine?
Corrosion can significantly impact the lifespan and efficiency of a diesel engine. Regular maintenance, including checking for signs of corrosion in fuel lines and components, can help prevent costly repairs and ensure reliable operation.
How can I create an effective maintenance schedule for my diesel truck?
To create an effective maintenance schedule for your diesel truck, consider factors such as mileage, operating conditions, and manufacturer recommendations. Include regular checks for engine oil levels, oil changes, filter replacements, and inspections of key components like the water separator and fuel system.
What are the key aspects of diesel maintenance for modern diesel engines?
Key aspects of diesel maintenance for modern diesel engines include regular oil and filter changes, checking fuel quality, inspecting the engine bay for leaks, and ensuring proper air filtration. Following these practices helps keep your diesel running smoothly.
How does basic diesel engine maintenance differ from that of a petrol engine?
Basic diesel engine maintenance differs from that of a petrol engine primarily in the fuel system and lubrication requirements. Diesel engines are renowned for their durability but require specific care, such as using the right diesel engine oil and maintaining service intervals.
What should you do to keep your diesel truck running efficiently?
To keep your diesel truck running efficiently, perform routine servicing, change your oil regularly, check and replace fuel filters, and empty the water separator. These steps ensure proper diesel engine maintenance and enhance engine lubrication.
Why is it important to change your oil in a modern diesel vehicle?
Changing your oil in a modern diesel vehicle is essential because it prevents decreased engine performance and prolongs engine life. Regular oil changes help remove contaminants and maintain optimal lubrication for the diesel engine’s components.
How often should you change your fuel filters in older diesel engines?
In older diesel engines, it is advisable to change your fuel filters every 10,000 to 15,000 miles, or as recommended by a qualified diesel mechanic. This practice helps prevent issues caused by contaminated diesel fuel.
What are the signs of decreased engine performance in a diesel vehicle?
Signs of decreased engine performance in a diesel vehicle can include rough idling, poor acceleration, excessive exhaust smoke, and unusual noises. Addressing these issues promptly with qualified diesel maintenance services can prevent further engine failure.
How can truck owners ensure proper care of their diesel engines?
Truck owners can ensure proper care of their diesel engines by adhering to a full diesel engine service schedule, which includes regular inspections, timely oil and filter changes, and monitoring fuel quality to prevent contamination.
What is the difference between servicing a diesel truck and a petrol truck?
The difference between servicing a diesel truck and a petrol truck lies in the complexity of the diesel engine’s fuel system and the need for specific maintenance practices. Diesel mechanics focus on aspects like turbo diesel components and enhanced lubrication requirements.
Why is it crucial to empty the water separator in a diesel vehicle?
Emptying the water separator in a diesel vehicle is crucial because accumulated water can cause corrosion and fuel contamination. Regularly checking this component helps keep your engine running smoothly and prevents common diesel engine issues.
How do modern diesel engines enhance engine lubrication compared to older models?
Modern diesel engines enhance engine lubrication through improved oil formulations and advanced filtration systems. These innovations allow for better protection against wear and tear, ensuring that even older diesel engines perform optimally when maintained correctly.